Fuel Cell systems
SOFC System Development History
SOFC System Development History (1)
The SOFC is a very advanced technology handling ceramic assemblies. Despite its difficulty, since the early stage, Osaka Gas has been engaged in its system evaluation, research, and development because it is expected to have the highest power generation efficiency as a fuel cell system.
During the period from 1987 to 1997, jointly with Tokyo Gas Co., Ltd. and Westinghouse (WH), a US firm, Osaka Gas evaluated SOFC power generation systems and developed cogeneration systems. The 3,000-hour test on a 3 kW tubular cell module in 1987 is said to have contributed to the startup of a number of SOFC research and development activities up to around 1990 in Japan.
After this, a 25 kW-class cogeneration system started operating in 1992, and after improvement of the cells in March 1995, it recorded the then world’s longest operating time of 13,194 hours. This SOFC cogeneration system, in which all of the power generation section, the fuel supply section, the exhaust heat recovery section, and the control section were assembled in one package, achieved an operating target of over 10,000 hours and observed a degradation rate of 0.1%/1,000 hours, including 11 start-and-stops. Thus, the system showed the most stable characteristics among all stationary fuel cell systems.
In the world’s first pressurized SOFC/GT unit operated by WH in 2000–2003 (WH’s generator business was later purchased by Siemens), Osaka Gas concluded a contract for the provision of operating data with WH, evaluating the commercial viability of high-efficiency power generation systems. Nonetheless, this system was not commercialized because of the costs incurred under the design and manufacturing conditions at the time.
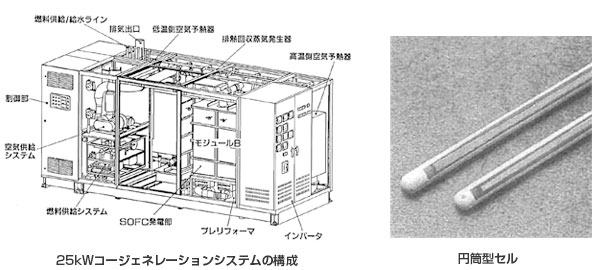
On the other hand, a planar-type SOFC has a higher power density than the tubular-type SOFC, promising high efficiency, downsizing, and cost reductions. Therefore, concurrently with the research into tubular-type systems, Osaka Gas was also engaged in a joint research project for planar-type SOFC with Murata Manufacturing Co., Ltd. (1993–1997). One problem with the planar type is its vulnerability to thermal strain, a defect that makes the cells prone to break when a number of cells are stacked to form a cell stack.
Osaka Gas solved this problem by stacking single cells with nickel felt into a unique structure, grouping five cells into a unit for checking its gas leakage and power output, thereby improving the reliability of the cells. These improvements allowed an 80-cell stack, made up of 16 series-connected five-cell units, to successfully undergo a 10-cycle heat cycle performance test, with the system exhibiting a maximum output of 1.3 kW. It was the first case in which a 1 kW-class stack was provided with heat cycle resistance.
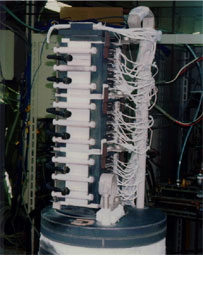
SOFC System Development History (2)
In 2004, Osaka Gas started joint development with Kyocera Corporation on residential 1 kW-class SOFC cogeneration systems. At the time, the general view was predominantly skeptical that the high-efficiency power generation characteristics of the SOFC could be achieved on a household scale. In fiscal 2005, Osaka Gas conducted Japan’s first experiment at an actual residence in the NEXT21 experimental housing project, technically demonstrating not only an operating power generation efficiency exceeding that of the utility power systems (average for fossil-fueled power, at the demand end) under conditions that followed the domestic power loads but also the feasibility of effectively using the exhaust heat. As a result, Osaka Gas considered use of SOFCs as a residential cogeneration system that would bring the highest power generation efficiency and decided to undertake the development of commercial units of this type.
Then, in fiscal 2006, Osaka Gas achieved a roughly 50% downsizing of the system volume after changing the rated output from 1 kW to 700 W in order to leverage the system’s characteristics, which fully bring about environmental and economic advantages while fitting the relatively small residential heat demand. Since fiscal 2007, Osaka Gas has been participating in the Demonstrative Research on Solid Oxide Fuel Cells project sponsored by the New Energy Foundation, and it has accelerated its effort toward commercialization, including improving the durability and reliability.
In March 2009, the project made another start in a four-company joint development with Toyota Motor Corporation and Aisin Seiki Co., Ltd., leveraging each company’s strength. Continuous and steady efforts to make durability and reliability improvements have led to the commercialization in April 2012.
SOFC System Development History (3)
After the launch of the first model in 2012, in 2013, Osaka Gas released a model with a self-sustaining power generation function that could continue to generate power even in the event of a grid outage. In 2014, the company released a model costing less than the previous model yet with higher added value, such as visualization of energy (e.g. amount of power generated), adding a remote control provided with wireless LAN capability to the line of products.
In 2016, by adopting cell stack durability improvement technology, the company had success in achieving both high power generation efficiency at 52% and durability. In addition, by employing a structure that contained a hot water storage tank and connected to the traditional gas water heater, it became possible to use the existing gas water heater as it was and install only the power generation unit as a retrofit. At the same time, in line with the full liberalization of the electricity retail market that took effect in April 2016, Osaka Gas was the first in Japan to introduce a program of purchasing electricity generated by the Ene-Farm type S but not consumed in the customer’s home (surplus electricity). The company has contributed to society’s overall CO2 emissions reduction, the diversification and decentralization of power sources promoted by the national government, and the flattening of electricity supply and demand peaks.
Subsequently, in 2018, the power generation efficiency was improved to 53.5%. Furthermore, Osaka Gas also provided additional IoT-based services, such as enabling voice operations via a smart speaker. In 2018, Typhoon Jebi hit the Kansai region, causing power outages in a large area, including Osaka and Hyogo. During this event, about 2,000 units of Ene-Farm type S (an estimate based on 853 units ascertained by the IoT function and the percentage of units equipped with the IoT function) generated electricity independently. These units were active during the grid outage, providing power for smartphone charging, lighting, hot water supply, and refrigerators, demonstrating the high resilience of Ene-Farm type S.
Subsequently in April 2020, the model’s power generation efficiency increased to 55% owing to the improved cell stack manufacturing process and through optimization of the control program. Furthermore, the model’s durability was improved from 10 to 12 years. Additionally, the cell stack and the power conditioner were downsized to make the equipment slimmer, greatly improving the ease of installation in condominiums where installation space is limited.
Durability Evaluation Technology of Osaka Gas
Since SOFCs basically operate 24 hours a day, it is essential to ensure durability and reliability for long-term operation.
Strict durability performance is required of both cell stacks and auxiliary parts. To meet the requirements, Osaka Gas conducts research and development consistently, ranging from elementary materials to fuel cell systems.
Related contents
TAG SEARCH
- Evolving residential gas appliances
- Evolving residential gas appliances Water heaters, space heaters, dryers Cooking appliances Smart Equipment Fuel Cell systems
- Evolving commercial and industrial gas appliances
- Evolving commercial and industrial gas appliances Cogeneration (CHP) units Air conditioning systems, kitchen appliances Bio, water treatment Industrial furnaces, burners Energy management, IoT
- Enhancing the safety and economic efficiency of LNG regasification
- Enhancing the safety and economic efficiency of LNG regasification Utilization of cold energy Plant materials Power generation technology
- Developing next-generation businesses through enterprising initiatives
- Developing next-generation businesses through enterprising initiatives Materials development Measurement Simulation, data analysis Food science Material evaluation
- Contributing to conserving the environment and achieving a carbon neutral society
- Contributing to conserving the environment and achieving a carbon neutral society Methanation Hydrogen, ammonia Biogas Energy management Renewable Energy
- Technologies of Group companies
- KRI, Inc. Osaka Gas Chemicals Group OGIS-RI Group