Industrial furnaces, burners
New Ceramic Tube Type Forging Furnace Equipped with a Regenerative Burner
- Overview
- 1: Energy saving (40% more energy-saving than conventional type)
- 2: Cost saving (half the running cost of electricity)
- 3: Automation and labor saving (furnace provided with a self-emptying function)
- 4: Reduced oxide scale (non-oxidation forging furnace)
- 5: Function to suppress the cooling of the end faces of workpieces to be discharged
- Related Material
Overview
The ceramic tube type forging furnace is structured to heat the outer surfaces of ceramic tubes by burner combustion. The workpiece is passed through the heated ceramic tube and is indirectly heated gradually to the required forging temperature. Indirect heating contributes to reduced oxide scale on the workpiece. With these features, it is a pusher type continuous heating forging furnace.
By mounting a regenerative burner on a ceramic tube type forging furnace and overcoming issues with the previous models, Osaka Gas and Asabe Kogyo Co., Ltd. jointly developed a ceramic tube type forging furnace equipped with a regenerative burner, which is more energy-saving and has higher performance. The furnace is available in three sizes: large, medium, and small.
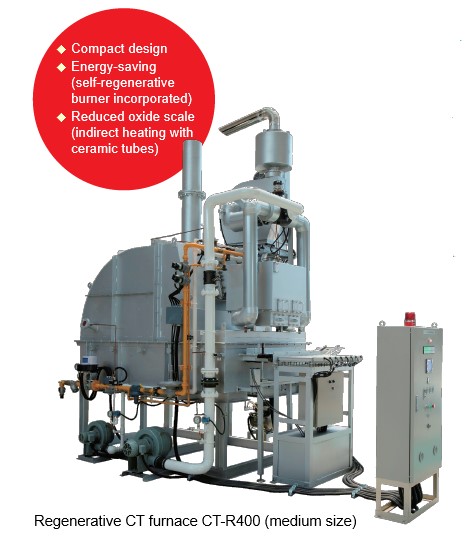
1: Energy saving (40% more energy-saving than conventional type)
A compact self-regenerative burner (manufactured by Osaka Gas) is employed to achieve energy saving.

2: Cost saving (half the running cost of electricity)
The running cost (energy cost) of the furnace is half that of a comparable induction heater (electric). A compact self-regenerative burner (manufactured by Osaka Gas) is employed to achieve energy saving.
3: Automation and labor saving (furnace provided with a self-emptying function)
An automatic workpiece discharge device with variable stroke (patent pending), newly developed, provides the furnace with a self-emptying capability. The device eliminates the need for discharging a dummy material or discharge operation by an operator with a push rod. (The automatic workpiece discharge device with variable stroke is installed as an option.)
The running cost (energy cost) of the furnace is half that of a comparable induction heater (electric).
4: Reduced oxide scale (non-oxidation forging furnace)
By injecting high-purity N2 (nitrogen gas) made by PSA into the ceramic tube through which the workpiece is passed, it is possible to create a non-oxidizing atmosphere and further reduce oxide scale on the workpiece (patent pending). (* The non-oxidizing system is installed as an option.)
5: Function to suppress the cooling of the end faces of workpieces to be discharged
A special stainless steel curtain is provided at the discharge end of the ceramic tube to prevent the entry of air and suppress the cooling of the end face of the workpiece to be discharged.
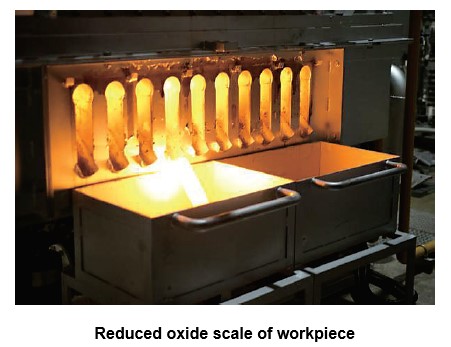
Related Material
Related contents
TAG SEARCH
- Evolving residential gas appliances
- Evolving residential gas appliances Water heaters, space heaters, dryers Cooking appliances Smart Equipment Fuel Cell systems
- Evolving commercial and industrial gas appliances
- Evolving commercial and industrial gas appliances Cogeneration (CHP) units Air conditioning systems, kitchen appliances Bio, water treatment Industrial furnaces, burners Energy management, IoT
- Enhancing the safety and economic efficiency of LNG regasification
- Enhancing the safety and economic efficiency of LNG regasification Utilization of cold energy Plant materials Power generation technology
- Developing next-generation businesses through enterprising initiatives
- Developing next-generation businesses through enterprising initiatives Materials development Measurement Simulation, data analysis Food science Material evaluation
- Contributing to conserving the environment and achieving a carbon neutral society
- Contributing to conserving the environment and achieving a carbon neutral society Methanation Hydrogen, ammonia Biogas Energy management Renewable Energy
- Technologies of Group companies
- KRI, Inc. Osaka Gas Chemicals Group OGIS-RI Group