Industrial furnaces, burners
Direct Hot-air Tumbler
Overview
Linen supply factories and other similar facilities often use batch-type large rotary drying ovens (hereinafter referred to as tumblers) to dry items such as towels and standard bedding after washing. For that purpose, the indirect steam heating system, which uses steam as a heat source to generate hot air, is widely used. Although the direct gas heating system has advantages such as lower running costs and less disturbance from the outside temperature than the steam system, the system’s introduction has been limited due to concerns over the discoloration (yellowing) of dyes attributed to NOx in combustion exhaust gas.
We addressed this challenge by developing an ultra-low NOx lean premixed burner (PHL burner), which features 10 ppm (O2 = 0%) or less NOx concentration, and establishing a design method for the duct to uniformly inject the burner combustion gas. Thus we have developed a compact, gas-fired direct hot-air tumbler with an elegant finish.
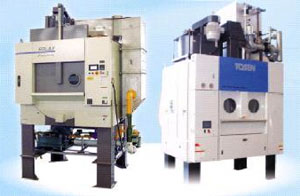
Operating Principle/Features
■ Development of ultra-low NOx lean premixed burner (PHL burner)
One of the causes of the yellowing of textile fabrics during drying is anthraquinone dyes used to produce bluish colors. The dyes react with NO2 and their blue colors fade, resulting in yellowish discoloring. Osaka Gas has developed an ultra-low NOx lean premixed burner (PHL burner), which features less than 10 ppm (O2 = 0%) NOx concentration, causing no yellowing, and applied it to a tumbler.
In terms of combustion performance, the tumbler has achieved the target NOx concentration of 10 ppm (O2 = 0%) or less by a large margin.
The PHL burner comes with combustion capacity options of 150 kW, 300 kW, and 600 kW according to tumbler capacity.
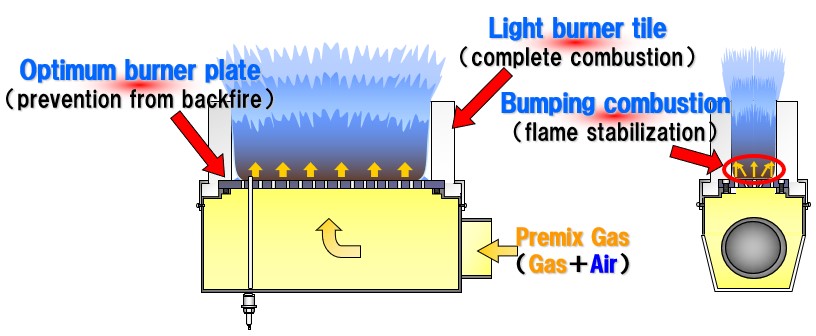
-
■ Advantages of direct hot-air tumbler
- 1. Energy savings
Compared with the indirect steam system, the direct hot-air system achieves greater energy savings, without losses resulting from steam piping, heat exchangers and drainage. - 2. Fast drying
The temperature of the hot air produced by the PHL burner is adjustable so that drying speed can be optimized (increased). - 3. Drastic steam consumption reduction
The direct hot-air system substantially reduces steam consumption. It enables independent drying on a holiday without requiring the boiler to be fired up. - 4. Stable drying
Ensures stable drying performance free from steam pressure variation caused by some other equipment in operation or from the effects of the outside air temperature. - 5. Extended fabric life
Reduced drying time translates to significantly extended fabric life. The ultra-low NOx PHL burner avoids yellowing of fabrics and ensures that items are finished with high quality.
- 1. Energy savings
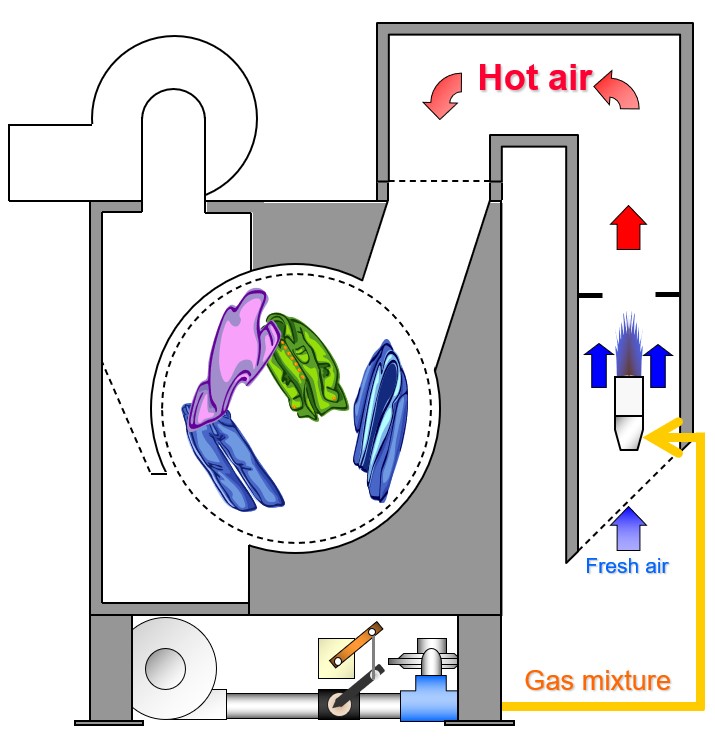
■ Safety design
The direct hot-air tumbler lets the combustion exhaust gas enter the tumbler drum directly from the gas burner. Accordingly, various safety measures are implemented to function in the event of failure.
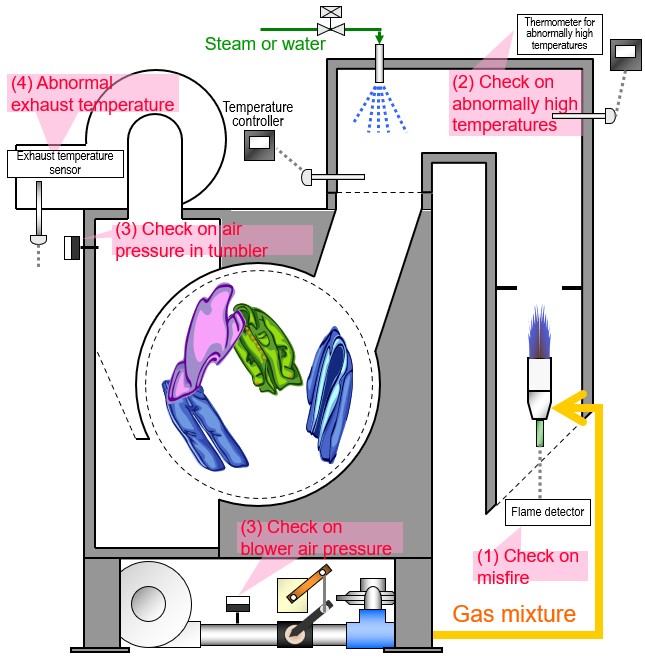
Related contents
TAG SEARCH
- Evolving residential gas appliances
- Evolving residential gas appliances Water heaters, space heaters, dryers Cooking appliances Smart Equipment Fuel Cell systems
- Evolving commercial and industrial gas appliances
- Evolving commercial and industrial gas appliances Cogeneration (CHP) units Air conditioning systems, kitchen appliances Bio, water treatment Industrial furnaces, burners Energy management, IoT
- Enhancing the safety and economic efficiency of LNG regasification
- Enhancing the safety and economic efficiency of LNG regasification Utilization of cold energy Plant materials Power generation technology
- Developing next-generation businesses through enterprising initiatives
- Developing next-generation businesses through enterprising initiatives Materials development Measurement Simulation, data analysis Food science Material evaluation
- Contributing to conserving the environment and achieving a carbon neutral society
- Contributing to conserving the environment and achieving a carbon neutral society Methanation Hydrogen, ammonia Biogas Energy management Renewable Energy
- Technologies of Group companies
- KRI, Inc. Osaka Gas Chemicals Group OGIS-RI Group